Разработка автоматизированной системы управления производством желтого фосфора в условиях
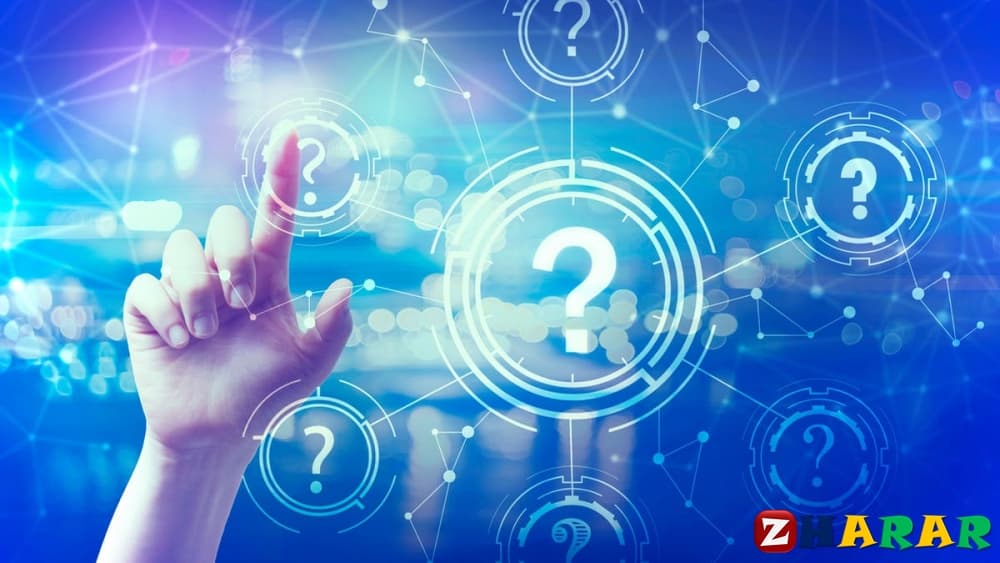
Содержание
Введение 9
1 Технологическая част
1.1 Краткая характеристика процесса окомкования фосфоритовой мело-
1.2 Общая характеристика производства и его технико-экономический
уровень 1
1.3 Характеристика производимой продукци
1.4 Описание технологических схем процесса 20
1.5 Технологические расчеты 21
Приложение Б,В,Г,Д
2 Специальная часть 27
2.1 Назначение и цель создания системы управления процессом окомко-вания
2.2 Процесс окомкования как объект управления 27
2.3.Существующее состояние автоматизации процесса хлорирования 31
2.4 Требования к системе управления в целом и по видам обеспечения 34
2.4.1 Общие требования 34
2.4.2 Требования к организационному обеспечению 34
2.4.3 Требования к информационному обеспечению 34
2.4.4 Требования к алгоритмическому обеспечению 36
2.4.5 Требования к техническому обеспечению 36
2.4.6 Требования к программному обеспечению 37
2.5 Описание автоматизируемых функций 38
2.6 Разработка математической модели 39
2.6.1.Математическое описание процесса окомкования 39
2.6.2 Математическая модель основных физико-математических законо-мерностей процесса
2.6.3 Разработка нечеткой модели управления процессом
окомкования 49
2.6.4 Разработка интеллектуальной подсистемы управления окомкования
фосфоритной мелочи 5
2.6.5 Формирование базы знаний интеллектуальной системы
2.6.6 Исследование нечеткой модели управления 54
2.6.7 Исследование нейросетевой модели 58
2.6.8 Исследование нейро-нечеткой модели
2.6.9 Анализ результатов исследования интеллектуальных моделей
управления подачей шихты и влажности шихты 65
2.7 Расчетная часть проекта
2.8 Содержательная постановка задачи управления 78
2.9 Информационное обеспечение АСУТП 8
2.10 Организационное обеспечение АСУТ
2.11 Разработка технического обеспечения 8
2.12 Разработка программного обеспечения
3 Экономическая часть
3.1 Технико-экономическое обоснование на внедрение АСУТП
3.2 Капитальные затраты на разработку и внедрение АСУТП 98
3.2.1 Затраты на заработную плату разработчиков 98
3.2.2 Капитальные затраты на приобретение приборов и средств вычис-лительной техники
3.2.3 Затраты на монтаж
100
4 Безопасность жизнедеятельности 103
4.1 Анализ опасных и вредных производственных факторов 103
4.1.1 Характеристика условий труда 103
4.1.2 Освещенность
4.1.3 Расчет освещенности 108
4.1.3 Шум и вибрация 108
4.2 Защитные мероприятия
4.2.1 Спецодежда и предохранительные приспособления 109
4.2.2 Защита от шума и вибрации 109
4.2.3 Электробезопасность 111
4.2.4 Защитное заземление 113
4.2.5 Пожаробезопасность
Заключение
Перечень сокращений
Список используемой литературы
Приложение А
Приложение Б
Приложение В
Приложение Г
Приложение Д
1 Технологическая часть
Краткая характеристика процесса окомкования фосфорито-вой мелочи Слово «агломерат» происходит от латинского слова agglomerаtus [2,4],
что дословно означает присоединенный, прибавленный. Агломерация –
процесс получения кусков (агломерата) путем окомкования мелкой руды с
топливом при высокой температуре горения. Задачей процесса окомкования
является подготовка высококачественного сырья для доменного производства
из концентратов обогащения руд, рудной мелочи колошниковой пыли
окалины, шламов, отсева агломерата и других железосодержащих материалов
путем окомкования их с соответствующим количеством топлива в прочные и
пористые куски (агломерат). Окатывание (либо создание окатышей) является
сравнимо новым, скоро развирающимся методом окускования рудных
материалов. Окатыванием называют процесс получения окатышей из влажных
концентратов в окомкователях с последующей сушкой иупрочняющим обжигом окатышей в обжиговых агрегатах. Окатыши – рудный
материал, полученный из мелкой (пылевидной) руды либо
тонкоизмельченных концентратов, в виде шарообразных гранул диаметром 2-
3 до 30 мм (традиционно 10-15 мм). Окатыши – твердые шарообразные тела,
полученные методом окомкования тонкоизмельченных рудных материалов с
добавкой связывающих веществ с флюсами либо без них с последующим
упрочнением методами обжига, цементации либо автоклавирование. По
соотношению содержания главных и кислых пород (основности) окатыши
разделяют на отфлюсованные (частично либо полностью) и неотфлюсованные
(окисленные). создание окисленных окатышей включает окомкование шихты
(получение сырых окатышей) в барабанных, тарельчатых либо чашевых
окомкователях и упрочнение их обжигом либо безобжиговыми способами. В
зависимости от использования добавок различают фосфориты, фосфато-
кремневые и остальные окатыши. Фосфоритовые окатыши, в которых часть
оксидов фосфора (до 95%) восстановлена до сплава, именуются фосфатные
(употребляются, основным образом, в электроплавильных печах для
получения качественного сплава).
Качество окатышей выражают огромным списком характеристик, отра-
жающих их характеристики и функциональные признаки. Традиционно их
группируют на следующие четыре признака: 1) химико-минеральный состав;
2) механические характеристики; 3) физико-химические характеристики и 4)
стабильность качественных характеристик. По химико-минеральному составу
окатыши делят на неотфлюсованные, отфлюсованные и доломитизированные.
Параметрами свойства, выражающих механические характеристики окатышей
являются: крупность, крепкость на разрушаемость и истираемость, содержа-
ние лимитируемого класса < 5мм и пористость.
В группу физико-химических параметров входят следующие признаки:
1) восстановимость; 2) крепкость при восстановлении (при разных температу-
рах: а – 600-800 oС; б – 800-950 oС); 3) газодинамические характеристики
расплава, измеряемые методом перепада давления при восстановлении; 4)
размягчаемость; 5) набухаемость.
Стабильность качественных характеристик оценивают по их колебаемо-
сти, которую регламентируют указанием двухвеличин: пределами колебаний
(±% от среднего значения) и количество проб, укладываемых в обозначенные
пределы.
Участок по производству окатышей состоит из отделений подготовки
шихты, окомкования и обжигового. Транспортная связь между машинами и
агрегатами отделений осуществляется ленточными конвейерами. Основным
компонентом для производства окатышей является тонко измельченный
влажный концентрат. Перевозка его обычным железнодорожным транспортом
сопряжена с существенными трудностями при разгрузке, особенно в зимнее
время. Поэтому фабрики окатышей стремятся располагать непосредственно
поблизости от обогатительных фабрик, что позволяет выдаваемый ими кон-
центрат направлять на окомкование конвейерным транспортом.
Рисунок 1.1 -Технологическая схема производства окатышей
1 – бункера, 2 – питатели, 3 – конвейер, 4 – смесительный барабан,
5 – конвейер, 6 – чашевый окомкователь, 7 – бункер, 8 – питатель,
9 – конвейер, 10 – укладчик, 11 – питатель, 12 – машина упрочняюще-
восстановительного обжига, 13 – грохот.
Холодные окатыши имеют высокую прочность, что позволяет их транс-
портировать на большие расстояния к доменным цехам. Принципиальная схе-
ма технологического процесса представлена на рисунке 1.1. Концентрат, из-
вестняк и возврат поступают в бункера 1, откуда питателями 2 в определен-
ных соотношениях выдаются на конвейер 3, направляющий шихтовые мате-
риалы в смесительный барабан 4, по выходе из которого шихта конвейером 5
транспортируется в гранулятор 6. Перед окомкователем к шихте добавляют
бентонит, подаваемый из бункера 7 питателем 8. В окомкователе происходит
образование окатышей, чему в значительной степени способствует вода, по-
даваемая в гранулятор через распыляющую форсунку. Выходящие из окомко-
вателя сырые окатыши транспортируются конвейером 9 к укладчику 10. С
помощью укладчика окатыши подаются в питатель 11, который загружает их
на машину 12 упрочняющего или упрочняюще-восстановительного обжига.
После охлаждения готовые окатыши перед отправкой на склад подвергаются
рассеву на грохоте 13.
Главные операции технологического процесса следующие:
1) Подача пульпы концентрата с обогатительной фабрики;
2) Сгущение и усреднение концентрата в жидком виде;
3) Фильтрация концентрата;
4) Измельчение известняка;
5) Бункерование;
6) Дозирование компонентов шихты;
7) Смешивание компонентов шихты;
8) Окомкование шихты (получение сырых окатышей);
9) Грохочение сырых окатышей;
10) Сушка и предварительный нагрев сырых окатышей;
11) Обжиг окатышей;
12) Грохочение обожженных окатышей;
13) Остывание обожженных окатышей;
14) Складирование и отгрузка готовых окатышей.
Рудной базой фосфорной промышленности Казахстана является место-
рождение фосфоритов бассейна Каратау. Добываемые на рудниках фосфори-
ты и фосфато-кремнитые флюсующие материалы по физическим и химиче-
ским свойствам не отвечают требованиям технологического регламента про-
изводства желтого фосфора и требуют приведения ряда подготовительных
операций: дробление, грохочение, усреднение, сушка и обжиг окусковывание
[1]. Основной проблемой переработки фосфоритов бассейна Каратау является
то, что в цикле рудник-завод в процессе добычи, транспортировки, переработ-
ки, руды образуется до 55-60% фосфоритовой мелочи крупности (10-0 мм).
Руда такой фракции не может подвергаться переработке в электропечах.
Для производства окатышей в цехе употребляют желе-
зорудный концентрат, доломитизированный известняк, глину бентонитовую,
активированный торф и газообразное топливо. Подготовка концентрата.
Пульпа подается по пульпопроводу, магнитно флокируется и поступает в сгу-
стители, где. Взвешенные твердые частицы (с содержанием твердого 30...45%)
осаждаются на дно и сгребаются к центру разгрузочной воронки. Сгущенный
продукт-пульпа с плотностью 55 ... 65 %. удаляется со дна сгустителя насоса-
ми и размагничивается. Потом перегоняется в резервуары с механическими
мешалками для усреднения. Из резервуаров насосами пульпа перегоняется в
распределитель принудительной подачи. Для поддержания неизменного дав-
ления в распределителе приводы насосов имеют бесступенчатую регулировку.
Подача пульпы на фильтр регулируется автоматом, так чтоб количество по-
ступающей пульпы соответствовало производительности фильтра. Для каж-
дой технологической полосы предусмотрено 10 фильтров, в том числе один
резервный. Влажность кека составляет 9.5%. Концентрат подается в дозиро-
вочные бункера, а распределение по бункерам делается при помощи плужко-
вых сбрасывателей. Дозирование и смешивание компонентов шихты. Концен-
трат, известняк, бентонит и торф при помощи автоматических весодозаторов
выдаются на сборный конвейер в заданной пропорции. Смешивание осу-
ществляется в роторном смесителе, установленном на ленте, а потом одно-
родная шихта поступает в барабанные окомкователти. Окомкование шихты.
За счет перекатывания материалов и поверхностного натяжения воды, которая
впрыскивается для регулирования процесса окомкования в барабане. Рост
размера гранул прекращается, когда в барабане не остается маленьких частиц.
Дальнейшее перекатывание материала в окомкователе обеспечивает механи-
ческое уплотнение окатышей, для транспортировки, загрузки на решетке и
тепловой обработки на ней без разрушения. Для получения нео6ходимой
влажности шихты, предусматривается подача воды в окомкователь. После
окомкования окатыши проходят грохочение на роликовом грохоте с разделе-
нием на 2 класса: минус 9,5мм и плюс 9,5мм. Окатыши с размером менее
9,5мм ленточными конвейерами возвращаются в окомкователь для дальней-
шей доработки. Сырые окатыши размером крупнее 9,5 мм. Подаются на роли-
ковый грохотукладчик с помощью которого делается дополнительно отделе-
ние мелочи и укладка кондиционных окатышей на колосники движущейся
решетки равномерным слоем высотой около 180 мм. Мелочь после роликово-
го укладчика возвращается на конвейер концентрата после фильтров. Сушка и
предварительный нагрев окатышей осуществляется на движущейся колосни-
ковой решетке. Окатыши проходят три зоны: сушка в восходящем потоке,
сушка в нисходящем потоке и предварительный подогрев в нисходящим по-
током. При сушке в восходящем потоке горячие газы с температурой 400oС
нагнетаются в слой окатышей снизу, выпаривают из окатышей воду и нагре-
вают слой до средней температуры приблизительно 230oС. Увлажненные га-
зы, покидающие слой после сушки в восходящем потоке, охлаждаются в слое
приблизительно до 93oС и после очистки пыли до санитарных норм выбрасы-ваются в атмосферу.
При сушке в нисходящем потоке газы с t 400oС проса-
сываются через слой сверху вниз. Целью данной операции является обеспече-
ние удаления воды с верхнего слоя окатышей для предотвращения разруше-
ния их в зоне предварительного нагрева. При предварительном нагреве газы с
температурой 1040 – 1050 oС просасываются через слой сверху вниз. Целью
данной операции является получение нужной прочности окатышей, при кото-
рой они могут быть подвергнуты обжигу во вращающейся печи без заметного
разрушения. Средняя температура окатышей после решетки -980oС. Тепловая
обработка окатышей на решетке осуществляется горячими газами, отходящи-
ми из вращающейся печи. Перекачка газов по зоне решетки осуществляется
тремя технологическими вентиляторами, из которых два просасывают газ
сверху вниз через слой окатышей в зоне предварительного нагрева, сушки
нисходящим потоком и подают его в зону сушки восходящим потоком и один
вентилятор отсасывает газ из колпака указанной зоны. Схемой предусмотрена
возможность сброса излишков газа, поступающего из вращающейся печи в
зону предварительного нагрева и подаваемого в зону восходящим потоком
(байпасная система). Решетка вооружена промежуточной сухой газоочисткой,
установленной перед вентиляторами зоны предварительного нагрева (цикло-
ны), мокрой очистки (скруббер) перед сбросным вентилятором зоны сушки
восходящим потоком. Обжиг окатышей осуществляется во вращающейся пе-
чи диаметром – 6700 мм, длинной – 45720 мм. Для обжига применяется при-
родный газ, который сжигается в торцевой горелке, установленной на разгру-
зочном конце печи. Обжиг окатышей в печи происходит за счет излучения
факела горелки и раскаленной футеровки печи, а также конвекционного теп-
лообмена межгазовым потоком циркулирующим противопотоком, через печь,
огнеупорной футеровкой и поверхностью слоя окатышей. Печь оборудована
вентилятором для подачи воздуха на сжигание газа и газорегуляторной стан-
цией, обеспечивающей давление газа перед горелкой не более 2кг/cм2. Ока-
тыши передвигаются вдоль печи за счет её вращения, при этом происходит
неизменное пересыпание слоя окатышей и равномерный их обжиг при хоро-
шей температуре 1260 + 15-30oС. После печи окатыши попадают на станцион-
ный охлажденный грохот, с помощью которого удаляются спеки окатышей
либо настыли с вращающейся печи крупностью 200 мм и более. После грохо-
чения окатыши подаются на остывание в кольцевой охладитель. Кольцевой
охладитель представляет собой решетку в форме кольца шириной 3111.5 мм и
средний диаметр (полу суммой внешнего и внутреннего диаметров) 20116.8
мм. В загрузочной части охладителя установлена разравнивающая стена для
формирования равномерного слоя окатышей высотой 762 мм. Охладитель
имеет привод бесступенчатой регулировки скорости, за счет чего осуществля-
ется автоматическая регулировка высоты слоя окатышей. Охладитель враща-
ется в горизонтальной плоскости и конструктивно разделен на три зоны: ра-
бочая зона, где происходит остывание окатышей, составляет 303 градуса
окружности; загрузочная зона - дуга в 25 градусов, разгрузочная зона-дуга в
32 градуса. Остывание окатышей осуществляется продувом холодного возду-
ха снизу вверх. Рабочая зона разделяется, в свою очередь, на две зоны: зона
рекуперационного остывания, в которой от окатышей отбирается 70....80 %
тепла и зона окончательного остывания, в которой температура окатышей до-
водится до 120oС. Из зоны рекуперационного остывания нагретый воздухпе-
редается во крутящуюся печь частично через загрузочный желоб охладителя и
частично по отдельному газопроводу, соединяющему свод рекуперационной
зоны остывания с разгрузочной частью печи. Из зоны окончательного остыва-
ния газы сбрасываются в атмосферу без предварительной очистки с содержа-
нием пыли не более 60 мг/м3. Забор охлаждающего воздуха осуществляется с
атмосферы. Работу кольцевого охладителя обеспечивают два охлаждающих
вентилятора, по одному на каждую зону остывания. Охлажденные окатыши
подаются на вибропитатель-грохот, где делается отделение класса плюс 50
мм, который убирается пластинчатым конвейером через особый желоб, за
пределы цеха в открытый штабель. Класс минус 50 мм (кондиционные ока-
тыши), системой ленточных конвейеров транспортируется на склад либо на
отгрузку. Схемой грузопотоков предусматривается возможность подачи ока-
тышей на склад, конкретно на погрузку в баржи либо в железнодорожные ва-
гоны, а также одновременная подача окатышей на погрузку конкретно с фаб-
рики и со склада в железнодорожные вагоны либо в баржи. Укладка готовых
окатышей на склад и отгрузка его со склада осуществляется соответственно
одноконсольным штабелеукладчиком и роторным заборщиком напольного
типа на рельсовом ходу импортной поставки.
Для нормального развития процесса грануляции тонких материалов, в
их объеме должны быть флуктуации по плотности и влажности, т.е. необхо-
димо наличие зародышевых центров. При окомковании тонкоизмельченных
материалов зародышевыми центрами служат отдельные комочки, в которых
поры заполнены водой. Комочки, обладая достаточной массой (в несколько
граммов», при ссыпании в грануляторе получают такой запас кинетической
энергии, которой становится достаточно для осуществления перестройки
структуры окатыша. Кроме того, сыпучий материал, увлажненный до состоя-
ния максимальной капиллярной влагоемкости, обладает пониженной проч-
ностью сцепления, что облегчает взаимное перемещение отдельных частичек
и получение плотной структуры комка.
Процесс образования зародыша и формирования окатыша при «сухом»
гранулировании (когда в окомкователь подают материал с влажностью мень-
ше оптимальной и недостающее количество воды) можно представить следу-
ющим образом. Капля воды, попавшая и слой материала за счет капиллярных
сил, сразу же начинает распространяться во все стороны, заполняя поры меж-
ду отдельными частичками. Предельный размер образующегося комочка пря-
мо пропорционален величине капли и обратно пропорционален пористости
слоя материала. Вода практически перестает рacпpocтраняться в сыпучем ма-
териале, как только влажность комочка достигнет величины максимальной
капиллярной влагоемкости. Это время измеряется несколькими секундами.
Очевидно, что размер комков определяется в первую очередь размером
капель воды, попадающих в слой.
При «мокром» гранулировании (когда в окомкователь подают материал
с влажностью, превышающей оптимальную, и некоторое количество сухого
материала) зародышевые центры образуются в результате разрушения «су-
харя» (обезноженного на вакуум-фильтрах концентрата).
В дальнейшем комочки в окомкователе в результате многократных ссы-
паний и ударов о неподвижный слой материала уплотняются - отдельные ча-
стички за счет взаимного перемещения укладываются более плотно.
При этом избыточная влага выдавливается на поверхность комочка, в
результате чего становится возможным дальнейшее присоединение к такому
комку сухих частичек.
По мере приближения частичек друг к другу толщина пленок связан-
ной воды становится все меньше, прочность
сцепления увеличивается как показано на рисунке 1.2.
Благодаря внешним динамическим воздействиям преодолевается
упругое сопротивление водной пленки, частички «захватываются» «моле-
кулярной ловушкой» и притягиваются друг к другу. Следует подчеркнуть, что
сближение частичек за счет уменьшения толщины адсорбированных пленок
возможно только в том случае, когда избыток воды поглощается на поверхно-
сти комочка, например, в результате присоединения новых частичек матери-
ала....
Введение 9
1 Технологическая част
1.1 Краткая характеристика процесса окомкования фосфоритовой мело-
1.2 Общая характеристика производства и его технико-экономический
уровень 1
1.3 Характеристика производимой продукци
1.4 Описание технологических схем процесса 20
1.5 Технологические расчеты 21
Приложение Б,В,Г,Д
2 Специальная часть 27
2.1 Назначение и цель создания системы управления процессом окомко-вания
2.2 Процесс окомкования как объект управления 27
2.3.Существующее состояние автоматизации процесса хлорирования 31
2.4 Требования к системе управления в целом и по видам обеспечения 34
2.4.1 Общие требования 34
2.4.2 Требования к организационному обеспечению 34
2.4.3 Требования к информационному обеспечению 34
2.4.4 Требования к алгоритмическому обеспечению 36
2.4.5 Требования к техническому обеспечению 36
2.4.6 Требования к программному обеспечению 37
2.5 Описание автоматизируемых функций 38
2.6 Разработка математической модели 39
2.6.1.Математическое описание процесса окомкования 39
2.6.2 Математическая модель основных физико-математических законо-мерностей процесса
2.6.3 Разработка нечеткой модели управления процессом
окомкования 49
2.6.4 Разработка интеллектуальной подсистемы управления окомкования
фосфоритной мелочи 5
2.6.5 Формирование базы знаний интеллектуальной системы
2.6.6 Исследование нечеткой модели управления 54
2.6.7 Исследование нейросетевой модели 58
2.6.8 Исследование нейро-нечеткой модели
2.6.9 Анализ результатов исследования интеллектуальных моделей
управления подачей шихты и влажности шихты 65
2.7 Расчетная часть проекта
2.8 Содержательная постановка задачи управления 78
2.9 Информационное обеспечение АСУТП 8
2.10 Организационное обеспечение АСУТ
2.11 Разработка технического обеспечения 8
2.12 Разработка программного обеспечения
3 Экономическая часть
3.1 Технико-экономическое обоснование на внедрение АСУТП
3.2 Капитальные затраты на разработку и внедрение АСУТП 98
3.2.1 Затраты на заработную плату разработчиков 98
3.2.2 Капитальные затраты на приобретение приборов и средств вычис-лительной техники
3.2.3 Затраты на монтаж
100
4 Безопасность жизнедеятельности 103
4.1 Анализ опасных и вредных производственных факторов 103
4.1.1 Характеристика условий труда 103
4.1.2 Освещенность
4.1.3 Расчет освещенности 108
4.1.3 Шум и вибрация 108
4.2 Защитные мероприятия
4.2.1 Спецодежда и предохранительные приспособления 109
4.2.2 Защита от шума и вибрации 109
4.2.3 Электробезопасность 111
4.2.4 Защитное заземление 113
4.2.5 Пожаробезопасность
Заключение
Перечень сокращений
Список используемой литературы
Приложение А
Приложение Б
Приложение В
Приложение Г
Приложение Д
1 Технологическая часть
Краткая характеристика процесса окомкования фосфорито-вой мелочи Слово «агломерат» происходит от латинского слова agglomerаtus [2,4],
что дословно означает присоединенный, прибавленный. Агломерация –
процесс получения кусков (агломерата) путем окомкования мелкой руды с
топливом при высокой температуре горения. Задачей процесса окомкования
является подготовка высококачественного сырья для доменного производства
из концентратов обогащения руд, рудной мелочи колошниковой пыли
окалины, шламов, отсева агломерата и других железосодержащих материалов
путем окомкования их с соответствующим количеством топлива в прочные и
пористые куски (агломерат). Окатывание (либо создание окатышей) является
сравнимо новым, скоро развирающимся методом окускования рудных
материалов. Окатыванием называют процесс получения окатышей из влажных
концентратов в окомкователях с последующей сушкой иупрочняющим обжигом окатышей в обжиговых агрегатах. Окатыши – рудный
материал, полученный из мелкой (пылевидной) руды либо
тонкоизмельченных концентратов, в виде шарообразных гранул диаметром 2-
3 до 30 мм (традиционно 10-15 мм). Окатыши – твердые шарообразные тела,
полученные методом окомкования тонкоизмельченных рудных материалов с
добавкой связывающих веществ с флюсами либо без них с последующим
упрочнением методами обжига, цементации либо автоклавирование. По
соотношению содержания главных и кислых пород (основности) окатыши
разделяют на отфлюсованные (частично либо полностью) и неотфлюсованные
(окисленные). создание окисленных окатышей включает окомкование шихты
(получение сырых окатышей) в барабанных, тарельчатых либо чашевых
окомкователях и упрочнение их обжигом либо безобжиговыми способами. В
зависимости от использования добавок различают фосфориты, фосфато-
кремневые и остальные окатыши. Фосфоритовые окатыши, в которых часть
оксидов фосфора (до 95%) восстановлена до сплава, именуются фосфатные
(употребляются, основным образом, в электроплавильных печах для
получения качественного сплава).
Качество окатышей выражают огромным списком характеристик, отра-
жающих их характеристики и функциональные признаки. Традиционно их
группируют на следующие четыре признака: 1) химико-минеральный состав;
2) механические характеристики; 3) физико-химические характеристики и 4)
стабильность качественных характеристик. По химико-минеральному составу
окатыши делят на неотфлюсованные, отфлюсованные и доломитизированные.
Параметрами свойства, выражающих механические характеристики окатышей
являются: крупность, крепкость на разрушаемость и истираемость, содержа-
ние лимитируемого класса < 5мм и пористость.
В группу физико-химических параметров входят следующие признаки:
1) восстановимость; 2) крепкость при восстановлении (при разных температу-
рах: а – 600-800 oС; б – 800-950 oС); 3) газодинамические характеристики
расплава, измеряемые методом перепада давления при восстановлении; 4)
размягчаемость; 5) набухаемость.
Стабильность качественных характеристик оценивают по их колебаемо-
сти, которую регламентируют указанием двухвеличин: пределами колебаний
(±% от среднего значения) и количество проб, укладываемых в обозначенные
пределы.
Участок по производству окатышей состоит из отделений подготовки
шихты, окомкования и обжигового. Транспортная связь между машинами и
агрегатами отделений осуществляется ленточными конвейерами. Основным
компонентом для производства окатышей является тонко измельченный
влажный концентрат. Перевозка его обычным железнодорожным транспортом
сопряжена с существенными трудностями при разгрузке, особенно в зимнее
время. Поэтому фабрики окатышей стремятся располагать непосредственно
поблизости от обогатительных фабрик, что позволяет выдаваемый ими кон-
центрат направлять на окомкование конвейерным транспортом.
Рисунок 1.1 -Технологическая схема производства окатышей
1 – бункера, 2 – питатели, 3 – конвейер, 4 – смесительный барабан,
5 – конвейер, 6 – чашевый окомкователь, 7 – бункер, 8 – питатель,
9 – конвейер, 10 – укладчик, 11 – питатель, 12 – машина упрочняюще-
восстановительного обжига, 13 – грохот.
Холодные окатыши имеют высокую прочность, что позволяет их транс-
портировать на большие расстояния к доменным цехам. Принципиальная схе-
ма технологического процесса представлена на рисунке 1.1. Концентрат, из-
вестняк и возврат поступают в бункера 1, откуда питателями 2 в определен-
ных соотношениях выдаются на конвейер 3, направляющий шихтовые мате-
риалы в смесительный барабан 4, по выходе из которого шихта конвейером 5
транспортируется в гранулятор 6. Перед окомкователем к шихте добавляют
бентонит, подаваемый из бункера 7 питателем 8. В окомкователе происходит
образование окатышей, чему в значительной степени способствует вода, по-
даваемая в гранулятор через распыляющую форсунку. Выходящие из окомко-
вателя сырые окатыши транспортируются конвейером 9 к укладчику 10. С
помощью укладчика окатыши подаются в питатель 11, который загружает их
на машину 12 упрочняющего или упрочняюще-восстановительного обжига.
После охлаждения готовые окатыши перед отправкой на склад подвергаются
рассеву на грохоте 13.
Главные операции технологического процесса следующие:
1) Подача пульпы концентрата с обогатительной фабрики;
2) Сгущение и усреднение концентрата в жидком виде;
3) Фильтрация концентрата;
4) Измельчение известняка;
5) Бункерование;
6) Дозирование компонентов шихты;
7) Смешивание компонентов шихты;
8) Окомкование шихты (получение сырых окатышей);
9) Грохочение сырых окатышей;
10) Сушка и предварительный нагрев сырых окатышей;
11) Обжиг окатышей;
12) Грохочение обожженных окатышей;
13) Остывание обожженных окатышей;
14) Складирование и отгрузка готовых окатышей.
Рудной базой фосфорной промышленности Казахстана является место-
рождение фосфоритов бассейна Каратау. Добываемые на рудниках фосфори-
ты и фосфато-кремнитые флюсующие материалы по физическим и химиче-
ским свойствам не отвечают требованиям технологического регламента про-
изводства желтого фосфора и требуют приведения ряда подготовительных
операций: дробление, грохочение, усреднение, сушка и обжиг окусковывание
[1]. Основной проблемой переработки фосфоритов бассейна Каратау является
то, что в цикле рудник-завод в процессе добычи, транспортировки, переработ-
ки, руды образуется до 55-60% фосфоритовой мелочи крупности (10-0 мм).
Руда такой фракции не может подвергаться переработке в электропечах.
Для производства окатышей в цехе употребляют желе-
зорудный концентрат, доломитизированный известняк, глину бентонитовую,
активированный торф и газообразное топливо. Подготовка концентрата.
Пульпа подается по пульпопроводу, магнитно флокируется и поступает в сгу-
стители, где. Взвешенные твердые частицы (с содержанием твердого 30...45%)
осаждаются на дно и сгребаются к центру разгрузочной воронки. Сгущенный
продукт-пульпа с плотностью 55 ... 65 %. удаляется со дна сгустителя насоса-
ми и размагничивается. Потом перегоняется в резервуары с механическими
мешалками для усреднения. Из резервуаров насосами пульпа перегоняется в
распределитель принудительной подачи. Для поддержания неизменного дав-
ления в распределителе приводы насосов имеют бесступенчатую регулировку.
Подача пульпы на фильтр регулируется автоматом, так чтоб количество по-
ступающей пульпы соответствовало производительности фильтра. Для каж-
дой технологической полосы предусмотрено 10 фильтров, в том числе один
резервный. Влажность кека составляет 9.5%. Концентрат подается в дозиро-
вочные бункера, а распределение по бункерам делается при помощи плужко-
вых сбрасывателей. Дозирование и смешивание компонентов шихты. Концен-
трат, известняк, бентонит и торф при помощи автоматических весодозаторов
выдаются на сборный конвейер в заданной пропорции. Смешивание осу-
ществляется в роторном смесителе, установленном на ленте, а потом одно-
родная шихта поступает в барабанные окомкователти. Окомкование шихты.
За счет перекатывания материалов и поверхностного натяжения воды, которая
впрыскивается для регулирования процесса окомкования в барабане. Рост
размера гранул прекращается, когда в барабане не остается маленьких частиц.
Дальнейшее перекатывание материала в окомкователе обеспечивает механи-
ческое уплотнение окатышей, для транспортировки, загрузки на решетке и
тепловой обработки на ней без разрушения. Для получения нео6ходимой
влажности шихты, предусматривается подача воды в окомкователь. После
окомкования окатыши проходят грохочение на роликовом грохоте с разделе-
нием на 2 класса: минус 9,5мм и плюс 9,5мм. Окатыши с размером менее
9,5мм ленточными конвейерами возвращаются в окомкователь для дальней-
шей доработки. Сырые окатыши размером крупнее 9,5 мм. Подаются на роли-
ковый грохотукладчик с помощью которого делается дополнительно отделе-
ние мелочи и укладка кондиционных окатышей на колосники движущейся
решетки равномерным слоем высотой около 180 мм. Мелочь после роликово-
го укладчика возвращается на конвейер концентрата после фильтров. Сушка и
предварительный нагрев окатышей осуществляется на движущейся колосни-
ковой решетке. Окатыши проходят три зоны: сушка в восходящем потоке,
сушка в нисходящем потоке и предварительный подогрев в нисходящим по-
током. При сушке в восходящем потоке горячие газы с температурой 400oС
нагнетаются в слой окатышей снизу, выпаривают из окатышей воду и нагре-
вают слой до средней температуры приблизительно 230oС. Увлажненные га-
зы, покидающие слой после сушки в восходящем потоке, охлаждаются в слое
приблизительно до 93oС и после очистки пыли до санитарных норм выбрасы-ваются в атмосферу.
При сушке в нисходящем потоке газы с t 400oС проса-
сываются через слой сверху вниз. Целью данной операции является обеспече-
ние удаления воды с верхнего слоя окатышей для предотвращения разруше-
ния их в зоне предварительного нагрева. При предварительном нагреве газы с
температурой 1040 – 1050 oС просасываются через слой сверху вниз. Целью
данной операции является получение нужной прочности окатышей, при кото-
рой они могут быть подвергнуты обжигу во вращающейся печи без заметного
разрушения. Средняя температура окатышей после решетки -980oС. Тепловая
обработка окатышей на решетке осуществляется горячими газами, отходящи-
ми из вращающейся печи. Перекачка газов по зоне решетки осуществляется
тремя технологическими вентиляторами, из которых два просасывают газ
сверху вниз через слой окатышей в зоне предварительного нагрева, сушки
нисходящим потоком и подают его в зону сушки восходящим потоком и один
вентилятор отсасывает газ из колпака указанной зоны. Схемой предусмотрена
возможность сброса излишков газа, поступающего из вращающейся печи в
зону предварительного нагрева и подаваемого в зону восходящим потоком
(байпасная система). Решетка вооружена промежуточной сухой газоочисткой,
установленной перед вентиляторами зоны предварительного нагрева (цикло-
ны), мокрой очистки (скруббер) перед сбросным вентилятором зоны сушки
восходящим потоком. Обжиг окатышей осуществляется во вращающейся пе-
чи диаметром – 6700 мм, длинной – 45720 мм. Для обжига применяется при-
родный газ, который сжигается в торцевой горелке, установленной на разгру-
зочном конце печи. Обжиг окатышей в печи происходит за счет излучения
факела горелки и раскаленной футеровки печи, а также конвекционного теп-
лообмена межгазовым потоком циркулирующим противопотоком, через печь,
огнеупорной футеровкой и поверхностью слоя окатышей. Печь оборудована
вентилятором для подачи воздуха на сжигание газа и газорегуляторной стан-
цией, обеспечивающей давление газа перед горелкой не более 2кг/cм2. Ока-
тыши передвигаются вдоль печи за счет её вращения, при этом происходит
неизменное пересыпание слоя окатышей и равномерный их обжиг при хоро-
шей температуре 1260 + 15-30oС. После печи окатыши попадают на станцион-
ный охлажденный грохот, с помощью которого удаляются спеки окатышей
либо настыли с вращающейся печи крупностью 200 мм и более. После грохо-
чения окатыши подаются на остывание в кольцевой охладитель. Кольцевой
охладитель представляет собой решетку в форме кольца шириной 3111.5 мм и
средний диаметр (полу суммой внешнего и внутреннего диаметров) 20116.8
мм. В загрузочной части охладителя установлена разравнивающая стена для
формирования равномерного слоя окатышей высотой 762 мм. Охладитель
имеет привод бесступенчатой регулировки скорости, за счет чего осуществля-
ется автоматическая регулировка высоты слоя окатышей. Охладитель враща-
ется в горизонтальной плоскости и конструктивно разделен на три зоны: ра-
бочая зона, где происходит остывание окатышей, составляет 303 градуса
окружности; загрузочная зона - дуга в 25 градусов, разгрузочная зона-дуга в
32 градуса. Остывание окатышей осуществляется продувом холодного возду-
ха снизу вверх. Рабочая зона разделяется, в свою очередь, на две зоны: зона
рекуперационного остывания, в которой от окатышей отбирается 70....80 %
тепла и зона окончательного остывания, в которой температура окатышей до-
водится до 120oС. Из зоны рекуперационного остывания нагретый воздухпе-
редается во крутящуюся печь частично через загрузочный желоб охладителя и
частично по отдельному газопроводу, соединяющему свод рекуперационной
зоны остывания с разгрузочной частью печи. Из зоны окончательного остыва-
ния газы сбрасываются в атмосферу без предварительной очистки с содержа-
нием пыли не более 60 мг/м3. Забор охлаждающего воздуха осуществляется с
атмосферы. Работу кольцевого охладителя обеспечивают два охлаждающих
вентилятора, по одному на каждую зону остывания. Охлажденные окатыши
подаются на вибропитатель-грохот, где делается отделение класса плюс 50
мм, который убирается пластинчатым конвейером через особый желоб, за
пределы цеха в открытый штабель. Класс минус 50 мм (кондиционные ока-
тыши), системой ленточных конвейеров транспортируется на склад либо на
отгрузку. Схемой грузопотоков предусматривается возможность подачи ока-
тышей на склад, конкретно на погрузку в баржи либо в железнодорожные ва-
гоны, а также одновременная подача окатышей на погрузку конкретно с фаб-
рики и со склада в железнодорожные вагоны либо в баржи. Укладка готовых
окатышей на склад и отгрузка его со склада осуществляется соответственно
одноконсольным штабелеукладчиком и роторным заборщиком напольного
типа на рельсовом ходу импортной поставки.
Для нормального развития процесса грануляции тонких материалов, в
их объеме должны быть флуктуации по плотности и влажности, т.е. необхо-
димо наличие зародышевых центров. При окомковании тонкоизмельченных
материалов зародышевыми центрами служат отдельные комочки, в которых
поры заполнены водой. Комочки, обладая достаточной массой (в несколько
граммов», при ссыпании в грануляторе получают такой запас кинетической
энергии, которой становится достаточно для осуществления перестройки
структуры окатыша. Кроме того, сыпучий материал, увлажненный до состоя-
ния максимальной капиллярной влагоемкости, обладает пониженной проч-
ностью сцепления, что облегчает взаимное перемещение отдельных частичек
и получение плотной структуры комка.
Процесс образования зародыша и формирования окатыша при «сухом»
гранулировании (когда в окомкователь подают материал с влажностью мень-
ше оптимальной и недостающее количество воды) можно представить следу-
ющим образом. Капля воды, попавшая и слой материала за счет капиллярных
сил, сразу же начинает распространяться во все стороны, заполняя поры меж-
ду отдельными частичками. Предельный размер образующегося комочка пря-
мо пропорционален величине капли и обратно пропорционален пористости
слоя материала. Вода практически перестает рacпpocтраняться в сыпучем ма-
териале, как только влажность комочка достигнет величины максимальной
капиллярной влагоемкости. Это время измеряется несколькими секундами.
Очевидно, что размер комков определяется в первую очередь размером
капель воды, попадающих в слой.
При «мокром» гранулировании (когда в окомкователь подают материал
с влажностью, превышающей оптимальную, и некоторое количество сухого
материала) зародышевые центры образуются в результате разрушения «су-
харя» (обезноженного на вакуум-фильтрах концентрата).
В дальнейшем комочки в окомкователе в результате многократных ссы-
паний и ударов о неподвижный слой материала уплотняются - отдельные ча-
стички за счет взаимного перемещения укладываются более плотно.
При этом избыточная влага выдавливается на поверхность комочка, в
результате чего становится возможным дальнейшее присоединение к такому
комку сухих частичек.
По мере приближения частичек друг к другу толщина пленок связан-
ной воды становится все меньше, прочность
сцепления увеличивается как показано на рисунке 1.2.
Благодаря внешним динамическим воздействиям преодолевается
упругое сопротивление водной пленки, частички «захватываются» «моле-
кулярной ловушкой» и притягиваются друг к другу. Следует подчеркнуть, что
сближение частичек за счет уменьшения толщины адсорбированных пленок
возможно только в том случае, когда избыток воды поглощается на поверхно-
сти комочка, например, в результате присоединения новых частичек матери-
ала....
Толық нұсқасын 30 секундтан кейін жүктей аласыз!!!
Әлеуметтік желілерде бөлісіңіз:
Facebook | VK | WhatsApp | Telegram | Twitter
Қарап көріңіз 👇
Пайдалы сілтемелер:
» Туған күнге 99 тілектер жинағы: өз сөзімен, қысқаша, қарапайым туған күнге тілек
» Абай Құнанбаев барлық өлеңдер жинағын жүктеу, оқу
» Дастархан батасы: дастарханға бата беру, ас қайыру
Соңғы жаңалықтар:
» 2025 жылы Ораза және Рамазан айы қай күні басталады?
» Утиль алым мөлшерлемесі өзгермейтін болды
» Жоғары оқу орындарына құжат қабылдау қашан басталады?